自動車の設計では、軽量化が最優先事項です。 これは、スチールをアルミニウムに置き換えたり、後部座席を間引いたりするようなことだけを言っているのではありません。
自動車の軽量化によって、0-60mph加速能力や最高速度に関してよりもはるかに深いレベルの価値を生み出しています。A地点からB地点に移動するための自動車材料をより賢く使用することによって、安全性、製造コスト、運用コスト、および環境の持続可能性に直接的な恩恵を与えることができます。
より軽量な車両は、その他のすべてが同条件の車両よりも、より高速な加速、より俊敏なコーナリング、より高い最高速度、より短い停止距離など、様々な高いレベルのパフォーマンスを達成します。
また、軽量車はより安全な車になる可能性があります。衝突性能は、運動エネルギーの散逸と運動量の移動に帰着します。どちらも質量に比例し、またどちらも変形可能で圧壊可能な中空構造が必要です(これについては後で詳しく説明します)。
軽量車は運転コストが安く、1マイルあたりの燃料や電力が少なくて済みます。燃料/電力の節約は、結果としてカーボン排出量が少なくなることを意味し、即ち環境上の利益になります。
複利的効果
より興味深いことは、これらの効果が組み合わされて、節約量が倍増するということです。シャーシ構造の軽量化により、モーターの小型軽量化や、ブレーキとサスペンションの軽量化が可能になります。これで車両全体の重量が大幅に減少し、シャーシを再検討してさらに軽量化できます。これはすべて、高いパフォーマンス、より安全でより効率的な車両への可能性につながります。
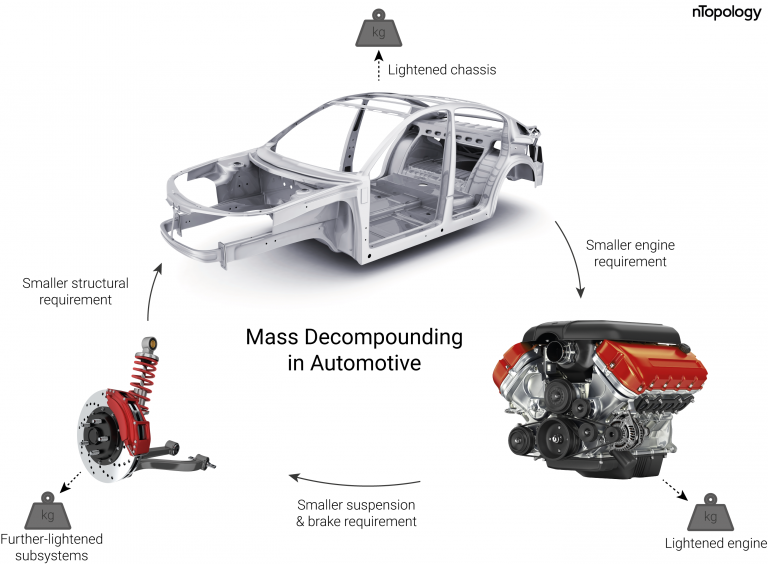
自動車設計での各コンポーネント間の質量影響分析。軽量のシャーシを使用すると、同じパフォーマンスを実現するために必要なエンジンのサイズが小さくなります。 つまり、ブレーキを小さくして軽量の車両を減速させ、さらに軽量化したシャーシでこれらの軽量のサブシステムをサポートします。これにより初期の軽量化タスクよりもはるかに大きな二次的な大量節約が可能になります。
これは、密度の高いバッテリーが車両の質量のかなりの部分を占める電気自動車では、さらに劇的になる可能性があります。電気自動車が(執筆時点で)まだ競争相手である内燃機関式の走行距離に追いつく途中なので、その1マイル伸長毎がディーラーからの重要な価値提案になります。
これらは、“二次的な質量節約”または“質量分解”と呼ばれます。興味がある場合は、MITおよびGeneral Motors [1]が提供するこのホワイトペーパーで、これらについて詳しく読むことができます。白紙から設計する例では、彼らは、(平均して)構造上の耐荷重部品の1ポンドの節約がサブシステム(ステアリング、ブレーキ、サスペンションなど)の1ポンド近く節約する機会を提供すると見積もっています。つまり1の効果が2になることを示しています。この数値は、設計サイクルが進行し、サブシステムが決定されるにつれて減少するため、これらの複合効果を最大化するために、可能な限り早期に軽量化を検討する必要があります。
車両のみでなく
軽量化は車両そのもの以外にも適用されます。組立ラインの数百万ポンドの治具と備品はすべて軽量化の候補です。材料の使用量が少ないだけでなく、より軽量なツールは、人間とロボットの双方にとって取扱が容易になり、高い生産効率を実現するための潜在的要素となります。最後に、軽量車のディーラーや顧客への輸送時には、軽量化による間接的なコスト削減が実現します。
軽量化は無料で実現できるのかというと、それは確かに違います。しかし、前述の価値命題により、今日の自動車業界でこれほど注目されている理由は明かです。
さらなる進歩
ほとんどの場合、新しいテクノロジーは少なくとも最初の実装時に、従来のものよりもコストがかかります。かつて、アルミニウムはコストの関係から航空宇宙専用の材料と見なされていて、自動車のBOM(部品表)では鋳鉄と鋼が長年主流でした。振り返ってみるとこれは驚くべきことであり、今日の私たちの車にはアルミニウムが非常に普及しています。私たちは複合材料で同じ現象の真っ只中にいます。少し前に、炭素繊維複合材料は航空宇宙とフォーミュラ1に追いやられ、最終的にはスーパーカー市場に流れ込みました。現在、それらは主流市場にも急速に拡大しており、一部のメーカーではすでに、家族向けのセダンや小さなハッチバックの大きなボディパネルを複合材料で製造しています。

軽量化に関する2つの関連する傾向:
1)新しい材料システムの実装タイムライン:一般に、軽量化を追求する場合、エンジニアはこれらの材料システムをおおよそこの順序で検討できます。
2)交換定数:車両の耐用年数を通しての軽量化の価値または有用性の指標
(つまり、燃費、ペイロード容量など)[2]。
これらの値は一般的なガイドラインとして役立ちますが、特定のケースがこのチャートの予期しない領域に到達する場合があります(たとえば、ハイエンドのレーシング自転車コンポーネントの宇宙船レベルの交換定数)。
ケーニグセグは2014年に、積層造形(AM)によるステンレス鋼製可変ターボチャージャーと、機械加工されたアルミニウムの前身よりも1キログラムも節約した3Dプリントされたチタン排気コンポーネントによって、最終製品を構成する部品への金属AM活用のトレンドを起こしたようです[3]。もちろん、これは1300馬力以上の数百万ドルの自動車ですが、自動車の金属AM時代の始まりを示しています。それ以来、いくつかの大きなメーカーが、はるかに大きな生産量での連続生産でAMを採用し始めました。この傾向は、軽合金や炭素繊維の場合と同様に、製造技術が成熟して安価になるまで続きます。
ただし、軽合金や複合材料とは異なり、AM技術の拡大により、部品の統合とAMプロセスのニアネットシェイプ加工に向けた技術進歩の両方により、かなりの量の工具(メーカーにとって時間とコストの両方にかなりの投資)が削減される場合があります。
課題は残っています
残念ながら、軽量化は、これらの新しく軽くて強い材料で置き換えれば済むというほど単純ではありません。それだけだは、その新しい材料またはプロセスの機会は十分に活用されないでしょう。複合材での「黒いアルミニウム」現象を思い出してください。複合材を使用して板金設計を再構築するだけでは、この新しい材料を最大限に活用できず、従来のシミュレーションや検証のアプローチも適切ではありませんでした[4]。 異方性、プライスタックの終端、サイズ/エッジ効果などはすべて、設計プロセスで考慮する新しいファクターでした。
複合材の利用初期段階では、エンジニアは複合材のマイクロメカニカルレベルの検討を始めたあと、ファイバーマトリックスの欠陥メカニズムなどを理解し、認証方法を確立する必要がありました。それを基にして、複合材による設計ガイドライン、繰り返し可能なワークフローとプロセスを確立する必要がありました。しかし、今日では複合材はいたるところに存在することとなり、もはやコンポジットなしの設計製造を想像することは困難です。
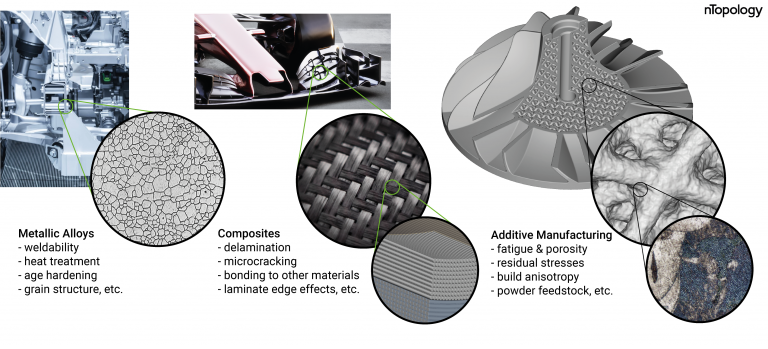
(「金属合金」の差し込み顕微鏡写真:[5])
同じことが、AMや高度なジェネレィティブデザイン/トポロジー・オプティマイゼーションによる有機的形状にも当てはまります。また、ラティス構造や材料構造創出に対してはさらに当てはまり、これらがもたらす潜在的な利益もはるかに大きくなります。このように、AMを活用した設計では制限があませんが(この時点でまだ残っている読者は、“制限がない”という表現はAMにとって完全に正確な表現ではないと思うかもしれませんが)、一方で、従来のモデリングツールでは、AMを活用するための設計と反復検討が非常に面倒であるという状況がありました。
モデルの作成が困難で時間がかかる場合は、シミュレーションと検証も難しくなります。最適なソリューションに近づくにつれて、使用する余地が少なくなり、安全率が低下するため、モデリング効率はさらに重要になります。これらの高度な製造技術と材料構造創出による相乗効果は、重量減だけの効果とは比較できないほど高くなるため、それらを効率的に活用するためのモデリングへの動機がさらに高まります。
トポロジー・オプティマイゼーション(場合によっては“ジェネレィティブ・デザイン)設計を行う場合、その結果は多くの場合、コンプライアンス最小化アルゴリズムによって形成されるソリッド形状になりますが、これがこの手法実装時の主な障害になります。ここでの問題は、そのソリッド形状では衝撃を受けてもスムーズに崩壊したり潰れたりしないこと、そのため衝突性能解析上から中空チューブ構造を必要とすることです。しかし、どのCADエンジニアも知っているように、複雑な有機形状部品のシェル化は、たとえそれが一定の壁厚であっても(ただし、材料の最適な分布である可能性は低いですが)、予想外に難しい作業になる可能性があります。従来、エンジニアは設計したものを製造するのに苦労してきました。しかし、AMを使用すると、逆になることがよくあります。AMでのみ製造できるような複雑なものを設計するのは大変なことです。
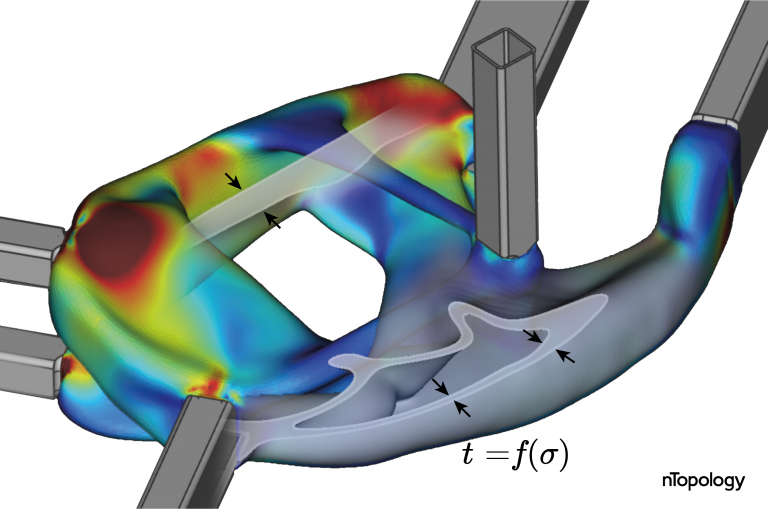
機会と展望
材料とプロセスの改善は順調に進んでおり、目覚ましい進歩を見せています。かつては法外に高額だった炭素繊維複合材のような技術はますます安価になり、チョップドファイバーの圧縮成形はすでに主流の自動車でビジネスケースを作っています。これと同様に、かつて懐疑論者が200 mmのビルドプレートエッジ長を超えることはないと言っていた、金属粉末ベッドフュージョンなどの当時のニッチテクノロジーは、現在複数のレーザー光源で1000 mmの領域に達しています。
ただし、高度な材料は、その特長を生かすに相応しい形を形成する場合にのみ効果を発揮します。トポロジーはこの戦いのひとつの側面にすぎません。現在ますます重大なボトルネックになっているもう1つの側面は、プロセスが断片化された上流工程向けの高価な設計ツール(CAD、CAM、CAEなど)にあります。
これらのツール間の各連携を実際に行おうとすると、驚くほどの時間(したがってコスト)が必要になります。形状最適化密度フィールドのネイティブジオメトリを再構築するために何日も費やされることや、耐衝撃性の要件でシェル化する場合、スケッチの拘束とオフセットに何週間も取り組んでいることを、ときどき耳にします。 後者はもちろん、壁の厚さを局所的に調整するために再メッシュと再検証が必要であり、うまくいった場合は、このプロセス全体の最後の反復作業になるでしょう(まれにあります)。これらの最後の数ポンドの重量を取り除くために必要な設計作業は、指数関数的に増加します。
従来からの材料で生産されている部分(鋳鉄製のブレーキディスクとエンジンブロックなど)について、モデリングやCADでの図面化などの既存のツールによる手順も存続するでしょう。しかし業界では、新しい材料と技術を活用した設計手法に基づいて開発された、強固で最新の設計ツールに対する明白なニーズがあります。
鋼、プラスチック、アルミニウム合金、マグネシウム合金、および炭素複合材がすべて同じ車両プラットフォームに共存しているため、混合材料設計がますます一般的になっています。非常に異なる材料を結合してハイブリッド化し、新しいレベルの自動車性能を達成するために学びつつあります。全ての目的を達成できるような万能な単一材料などはないのですから。
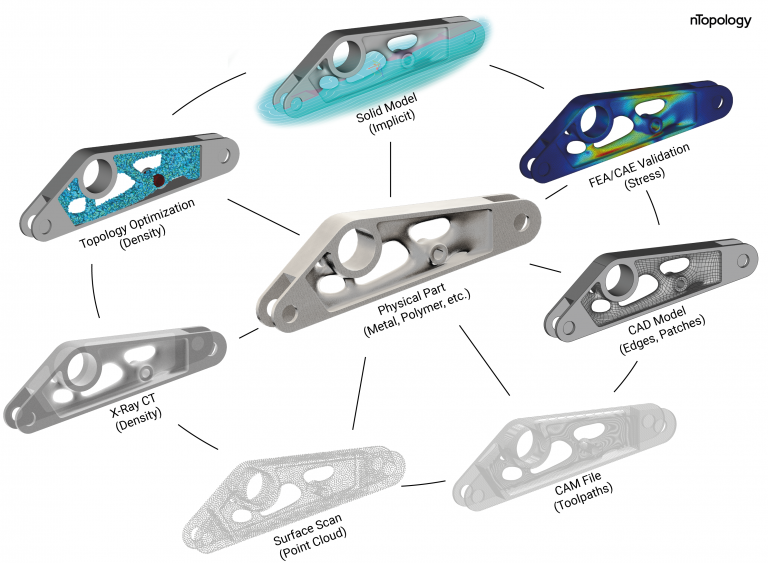
軽量化の追求では、混合材料に関してと同じことが設計ツールにも当てはまります。CADからのサーフェス、FEAからのメッシュ、CAEからの密度フィールドまたは応力結果、スキャンデータやデジタル画像化されたひずみなどの実世界の測定など、複合的なデータソースがあります。物理的な材料と同様に、これらもデジタルで合成および融合して、新しいレベルのパフォーマンスを実現できます。
この混合材料、多目的設計、および最適化プロセスを実行するための新しいツールが必要です。最適な場所で使用されているすべての複合データソースを考慮してください。ここにコンピューテショナル・モデリングが適合し、エンジニアリングプロセスに関連する多くの要素と測定値を1つの高性能設計表現に合成できるエンジニアリング設計へのこのデータ融合アプローチを可能にします。設計へのこの新しい多要素アプローチにより、自動車で利用可能な多くの軽量化手法を同時に活用し始めることができます。
自動車の軽量化に関するコンテンツをもっと探していますか? ヨーロッパのグリーンディールとそれがドイツの自動車メーカーに与える影響について、Fabian Gruppが何と言っているかを確認してください。 是非、今ご覧ください。
参考文献
[1] E. Alonso, T.M. Lee, C. Bjelkengren, R. Roth, R.E. Kirchain, “Evaluating the Potential for Secondary Mass Savings in Vehicle Lightweighting”, Environmental Science and Technology, 2012. [2] M.F. Ashby, Materials Selection in Mechanical Design, 5e, 2016 [3] 3D Printing: Titanium, Carbon Fiber, & The One:1 – /INSIDE KOENIGSEGG [Video Interview, The Drive, 2014] [4] S. Black, “Getting To Know “Black Aluminum”: An introduction to CFRP”, Modern Machine Shop, 2008. [5] Image from: Grain Size Analysis in Metals and Alloys, Olympus Industrial Resources.R.Heuss, N. Muller, W. van Sintern, A. Starke, A. Tschiesner, “Lightweight, heavy impact”, McKinsey & Company, “Advanced Industries” Series, 2012.
A.Weber, “Lightweighting Is Top Priority for Automotive Industry”, Assembly Magazine, 2018. Link